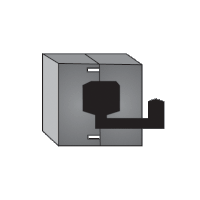
Die Tool Manufacturing
A single or multi cavity of product is prepared in form of metal with adding all the contraction of wax & metal to make wax pattern, which will match shape & dimension of casting parts.
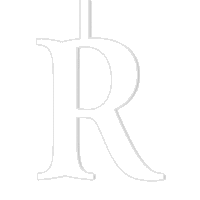
Wax Injection
Virgin Or Re-Claimed wax in semi liquid form is injected in single or multi-cavity die tool by using Wax injection press (Fully Auto, Semi Auto, Manually Operated). These processes will give wax pattern which will be the model of parts intended for casting.
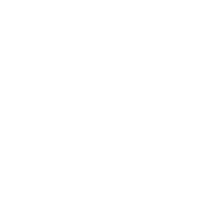
Wax Pattern Assembly
Clean wax pattern are assembled on runner with all handling and knock off arrangements for next process. this process is backed by methoding Engineer.
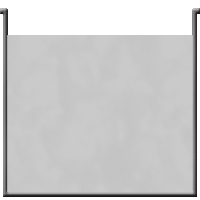
Shell Building
First, Primary Coating applied on wax pattern assembly by using ceramic slurry & sand, surface finish depends on primary coating & wax pattern surface. Then repeated back-up coating will apply with defined drying time to form a self supporting shell.
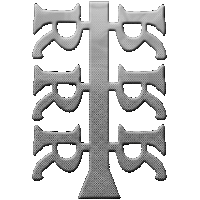
De Waxing
At De-waxing stage wax is melted out by applying steam pressure (Using Autoclave). Now, shells having cavities inside.
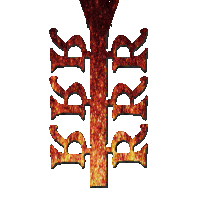
Melting
Shells are preheated at specific temperature & time. Specific molted metal are melt in induction melting furnace. De-gassed & De Slaged molted metal poured in preheated shells at specific temperature.
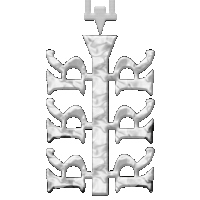
Knock Out
After cooling of cast shells, ceramics are removed by mechanical vibration and then parts are separated by cut-off machines or gas-arc cutting machines.

Heat Treatment
Castings are heat treated in house, according to the required standard in programmable heat treatment furnace.
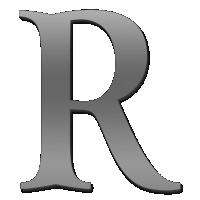
Fettling
heat treated parts are send for gate grinding & surface cleaning depending upon requirement of finish products.
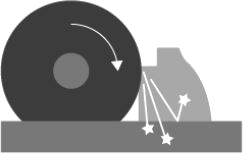
Machining
Castings are machined inhouse using various numerical control CNC, VMC and VTL machines to achieve dimensional accuracy as per the drawings.
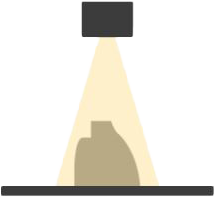
Testing
The parts are inspected for surface and sub-surface defects. Visual and liquid penetrant inspection is done for surface defect identification. Radiography and magnetic particle inspection is done for sub surface defect detection.Pressure testing insures leak free components.
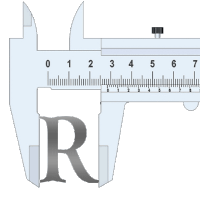
Final Inspection
Finished products of investment casting are inspected visually & dimensionally as per customer supplied drawing, purchase order & technical data sheet.